Scania use case shows benefits of Eclipse Arrowhead approach
The Combient Smart Production forum held earlier this year saw a presentation that clearly demonstrated the true potential of the Eclipse Arrowhead approach in a practical setting at Swedish manufacturer Scania’s plant for producing steel side beams in Luleå, northern Sweden.
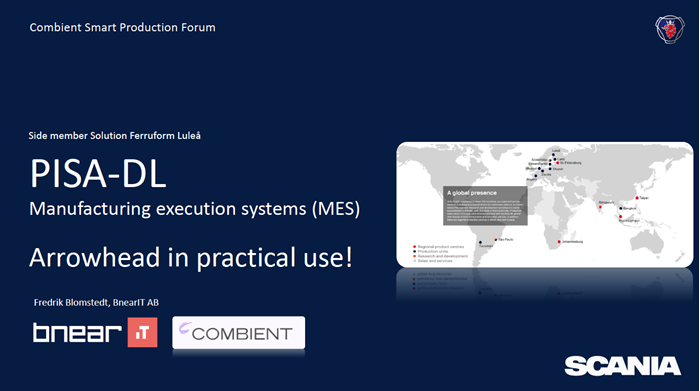
In the presentation, Fredrik Blomstedt of BnearIT AB, outlined the project that saw Scania’s previous management execution system replaced with a modern system that was more adapted to current and future production conditions. Management execution systems (MES) control various elements of the manufacturing process (inputs, personnel, machines, and support services) and work in real time to provide decision makers with data on how current conditions on the factory floor can be optimized to improve production output. The more we are able to optimize production based on the exact conditions on the production floor at a given time, the more we are able to use key variables in the manufacturing process to their maximum current potential. Scania’s previous system, RF-MES, consisted of old hardware that was becoming increasingly difficult to find parts for, it relied on source code that did not allow existing functionality to be easily upgraded or replaced to meet the demands of the current situation. This meant that the system in general was unable to be fully adapted to new requirements at the same time as existing hard dependencies on data storage also reduced the efficiency of the entire system. In addition, maintenance was time consuming and labour intensive for IT-operations personnel.
The goals of the new project were to replace the existing MES and provide a solution that would be flexible and able to adapt quickly to changing requirements, that would have lower development costs, be easier to maintain, have well-defined boundaries to create a dynamic, modular system and be less personnel intensive to maintain. By increasing compatibility between systems and components necessary information would be exchanged with minimal integration. This would increase coordination of resources and applications and increase the collaboration between business and technology while also reducing dependency on any specific supplier, manufacturer or technology, thus allowing for Best of Breed solutions.

With a careful system design based on service oriented architecture, Eclipse Arrowhead was able to meet all of the project requirements providing a system that could make use of existing components, be adaptable and also be easier to maintain. The solution included seven MES-level systems (one of which was operating in six instances), 26 services, 5 ERP systems, 4 SCADA systems and a range of technologies (MSMQ, MQTT, REST, FILE) coordinated through Eclipse Arrowhead’s service registry, orchestration and authorization suites. Eclipse Arrowhead’s service oriented approach led to a system composed of smaller, more clearly defined components with fewer requirements per component. Smaller components are easier to describe, verify and seamlessly deploy. In addition, they allow small adjustments and upgrades to a system to be made at relatively low cost in a way that allows development to suit the given needs at a particular time. It also allows reuse and continued integration of legacy systems, meaning that systems can be upgraded to meet current demands without the need for changing the building blocks (i.e. the components). Eclipse Arrowhead’s focus on interoperability also means that systems of services with loosely coupled or decoupled life cycles for each component can be created. This requires fewer financial and personnel resources than traditional approaches where entire systems need to be updated or restructured, these systems are often dependent on specific suppliers, technologies and products and are resource intensive.
The result can be described not simply as an IT project, but as a journey of business transformation. During the two first weeks of operation the new system broke three daily production records. Key findings from the project were that distributed and centralized operations could operate in tandem with centralized IT-operations and distributed systems of “small functions”, that governance could simultaneously be top-down and bottom-up, focusing on a disciplined coordination of services and clear descriptions as well as ensuring a system based on loose coupling, late binding and lookup. The approach also allows the development of a cost-efficient, future proof system allowing the reuse of existing investments (operational technology) with incremental targeted evolution (information technology). The project is an important step in the journey toward greater implementation of Industry 4.0.